Chromium Carbide Powder
We produce and stock customizable chromium carbide (Cr3C2, Cr7C3, Cr23C6) powders providing extreme hardness, low coefficient of friction surface finish, high wear resistance, and excellent oxidation/corrosion resistance.
Chemical Formula
Cr3C2, Cr7C3, Cr23C6
Synonyms
Chromium carbide, chromic carbide, methanidylidynechromium
Applications
- Corrosion resistant structural parts and coatings. Parts and coatings requiring oxidation and corrosion resistance such as valve seats, valve orifices, bearings, and seals.
- Wear surface (wear resistant) parts and coatings. Parts and coatings that undergo fretting, abrasion, cavitation, and particle erosion such as cyclones, fan blades, turbine blades, liners, chutes, hoppers and feeders.
- Welding Rod/Wire Filler. Iron-based wires coated with chromium carbide in an iron-based matrix material to produce extremely wear resistant deposits using the oxy-acetylene welding process.
- Additives. Our chromium carbide powder is added to other sintered carbides to inhibit grain growth during pressing and sintering.
Fabrication Methods
- Thermal Spray Process - High Velocity Oxygen Fuel (HVOF). Chromium carbide powders can be thermal sprayed to form hardface coatings on surfaces requiring increased corrosion resistance and wear resistance. Chromium carbide coatings are often made in a nickel-chromium mix.
- Powder Metallurgical (P/M). Chromium carbide powders are pressed into parts through hot or cold pressing and sintering.
Properties
- Molar Mass: 180.01 g/mol
- Density: 6.65-6.68 g/cm3
- Melting Point: 1250°C, 1665°C, 1895°C
- Boiling Point: 3800°C
- Hardness: 1735 Knoop
- Young's Modulus: 373 GPa
- Thermal Conductivity: 190 W/m·°C
- Appearance: gray powder
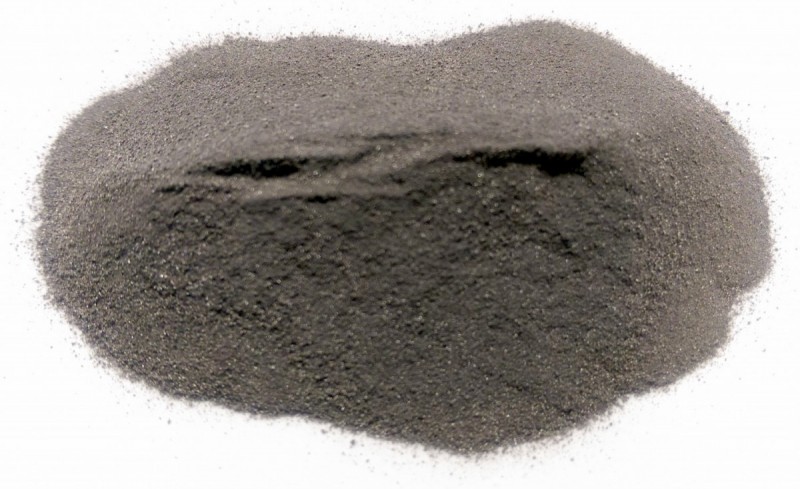